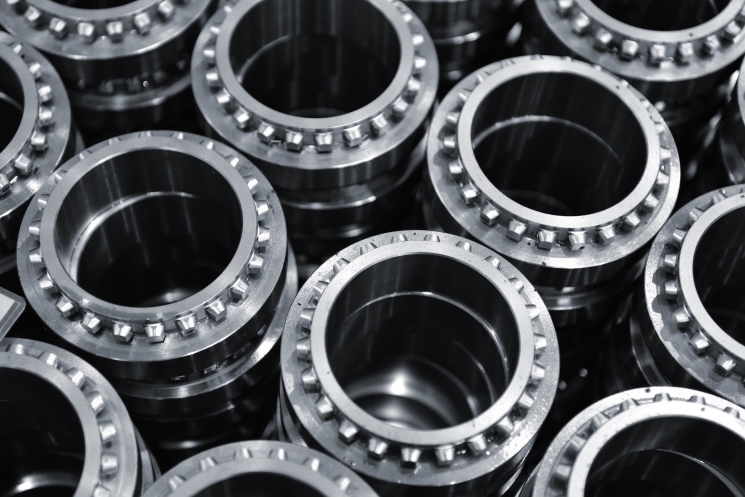
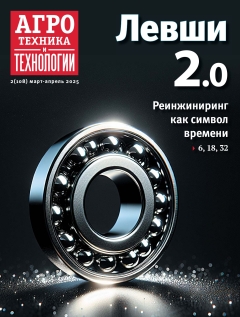
Журнал «Агротехника и технологии»
Процесс замещения иностранного оборудования и комплектующих для пищевой промышленности и сельского хозяйства российскими аналогами сопровождается рядом серьёзных вызовов, преодоление которых требует системного подхода и государственной поддержки. Каким образом государство стимулирует развитие отечественных производств, что думают о программах поддержки машиностроительные предприятия, которые занимаются реинжинирингом, и с какими вызовами они сталкиваются? Об этом журналу «Агротехника и технологии» рассказали эксперты и участники рынка
Обратный инжиниринг — это комплекс технологий, аппаратных и программных средств, которые позволяют создавать оборудование, комплектующие, а также разрабатывать конструкторскую документацию на основе готового образца.
Однако зачастую в таких случаях у конструкторов нет информации о первоначальных материалах, покрытиях, форме изделия до износа и технологиях изготовления, рассказали «Агротехнике и технологиям» в пресс-службе Минпромторга. Как правило, используются данные, полученные по результатам изучения готовой продукции, а в процессе реинжиниринга наиболее актуальные технические или дизайнерские решения могут быть доработаны под новые требования и условия.
При этом, подчёркивают в ведомстве, реинжиниринг значительно сокращает временные и материальные затраты, которые необходимы при разработке изделия с нуля. Кроме того, современная технологическая и программная база позволяет автоматизировать большую часть процессов и повысить их производительность.
В Минпромторге также обратили внимание, что в случае обратного инжиниринга речь идёт не о прямом копировании, а о создании продукции с улучшенными потребительскими свойствами по сравнению с оригиналом. Как объяснили в пресс-службе ведомства, изделия адаптируются под запросы заказчиков за счёт использования совершенно иных материалов и технологических процессов, нежели в исходном образце. Это позволяет повысить надёжность и производительность новой отечественной продукции без нарушения патентных прав. «И что важно, компетенции и технологии остаются в России», — добавили представители Минпромторга.
Однако, отметили в ведомстве, необходимо учитывать, что обратный инжиниринг подразумевает значительные затраты на оборудование и программное обеспечение. Кроме того, не всегда есть возможность получить для изучения оригинальное изделие, поскольку ряд комплектующих используется в производстве «штучно», и их невозможно направить в лабораторию или инжиниринговый центр без остановки производственной линии. Также, по словам представителей пресс-службы, для эффективности обратного инжиниринга важно наличие унифицированной потребности на рынке.
Именно поэтому в настоящее время Минпромторгом осуществляется поддержка проектов, направленных на импортозамещение и стимулирование развития отечественных производств на всех этапах жизненного цикла продукции — от разработки до реализации.
Одна из системных мер, направленная на создание инновационной импортозамещающей продукции, — это субсидирование до 70% затрат на проведение НИОКР.
Как объяснили представители Минпромторга, в рамках механизма поддержки компенсируются, в том числе, расходы на оплату труда, материальные расходы (на закупку испытательного оборудования, комплектующих, сырья и материалов, аренду зданий, сооружений), расходы на производство опытной партии продукции и её тестирование, сертификацию и регистрацию, а также на испытания.
«При этом производитель, получивший поддержку по этому направлению, берёт на себя обязательства по реализации созданной в рамках НИОКР продукции в 5 раз больше, чем размер предоставленной субсидии», — рассказали в пресс-службе Минпромторга.
Также, продолжили в ведомстве, реализуется механизм субсидирования до 60% затрат на проект, в рамках которого создаются новые виды оборудования или модернизируются уже выпускаемые. «Обязательным условием для предоставления этой субсидии является привлечение научной организации. В этом случае производитель берёт на себя обязательство по реализации созданной в рамках НИОКР продукции в 3 раза больше, чем размер полученной субсидии», — пояснили в Минпромторге.
Кроме того, добавили представители ведомства, действует программа предоставления грантов на обратный инжиниринг критических комплектующих изделий, необходимых различным отраслям промышленности. Оператором является АНО «Агентство по технологическому развитию».
Руководитель проектов Центра компетенций импортозамещения в промышленности Агентства по технологическому развитию (АТР) Винера Абдулова рассказала о том, как строится работа с участниками рынка.
Прежде всего, российский потребитель комплектующих, сырья, материалов должен направить в агентство письмо — обоснование критичности запроса. По итогам рассмотрения агентство включает то или иное наименование в перечень приоритетных комплектующих и организует конкурсный отбор разработчиков.
Как сообщила Винера Абдулова, по условиям программы государство финансирует до 80% затрат на разработку, в том числе, изготовление опытных образцов. Максимальная сумма гранта составляет 150 млн рублей.
«Исполнитель, в свою очередь, берёт на себя обязательство разработать конструкторскую документацию и передать её в АТР в пользу России. В дальнейшем АТР направляет её квалифицированному производителю для организации серийного выпуска», — объясняет специалист.
По оценке ассоциации «Росспецмаш», программа предоставления грантов на обратный инжиниринг комплектующих реализуется достаточно активно. Согласно данным ассоциации, уже запущены сотни проектов в разных сегментах машиностроения и налажен выпуск целого ряда комплектующих.
Кроме того, добавляют в «Росспецмаш», локализация импортных комплектующих для машиностроения реализуется в рамках специальных инвестконтрактов, субсидирования НИОКР и программ Фонда развития промышленности.
По словам Винеры Абдуловой, за три года действия программы грантов на обратный инжиниринг Агентством по технологическому развитию было поддержано 70 проектов для отраслей сельскохозяйственного и пищевого машиностроения с объёмом финансирования 1,3 млрд рублей.
Кроме того, как рассказала Винера Абдулова, с января 2024 года АТР совместно с Минсельхозом и Минпромторгом реализует пилотный проект по обратному инжинирингу оборудования и комплектующих изделий для пищевой промышленности и сельского хозяйства. Отраслевая направленность достаточно широкая и включает в себя более 12 направлений: птицеводство, мясопереработку, производство молока, хлеба, сахара, сельхозтехники и комплектующих и другие.
Несколько проектов, сообщила Абдулова, уже успешно реализованы.
Например, организован серийный выпуск блока подшипников в сборе для перосъёмной машины MEYN. Заявителем выступил агрохолдинг «Дороничи», исполнителем — компания «Мезон».
Помимо этого, компанией «Ос-Нова» (Усть-Лабинск, Краснодарский край) была изготовлена элеваторная камнеловушка (аналог немецкой Glass-Wolff), которая используется при обработке сахарной свёклы — она улавливает камни при сортировке. Эта камнеловушка поставлена на семь площадок компании «Русагро».
А компанией «Мелмашком» (Мелитополь, Запорожская область) изготовлены шестерни межвальцовой передачи вальцевального станка, предназначенного для измельчения зерна и промежуточных продуктов размола пшеницы. Они применяются в составе комплекта оборудования на мукомольных предприятиях с увеличенным выходом муки и ранее поставлялись из Могилёв-Подольского машиностроительного завода (Украина). Один комплект шестерён изготовлен и поставлен на ЛКХП Кирова (Ленинградский комбинат хлебопродуктов им. С. М. Кирова).
В ближайшей перспективе наладить взаимодействие с Минпромторгом планируют и в «ТДНТ ИНЖИНИРИНГ», где сегодня для реинжиниринга используют только собственные ресурсы. Об этом сообщил директор компании, руководитель научно-производственного комплекса «ТДНТ ИНДАСТРИАЛ» Марат Копылов.
Он рассчитывает, что сотрудничество окажется взаимовыгодным и позволит предприятию решать больше задач в области реверс-инжиниринга как для пищевой промышленности, так и для других индустрий, поскольку ТДНТ ИНЖИНИРИНГ обладает серьёзным опытом производства деталей и компонентов для других отраслей промышленности, таких как авиационная и космическая.
«Недавно у нас состоялись переговоры с представителями Минпромторга о перспективах сотрудничества, и для нас важно, что представители ведомства готовы к открытому, продуктивному диалогу, а государство уделяет особое внимание доступности оборудования и вопросам импортозамещения», — поделился Марат Копылов.
Как отмечает директор Краснокамского ремонтно-механического завода (КРМЗ) Дмитрий Теплов, Минпромторг принял верное решение поддержать российский реинжиниринг, помочь в импортозамещении комплектующих, выявляя потребности производителей со всей России, размещая на производствах заказы больших объёмов. Но это оказался небыстрый процесс.
Так, ещё в 2021 году КРМЗ совместно с другими производителями из ассоциации «Росспецмаш» направили в Минпромторг запрос на производство карданных валов. «Пока этот вопрос решается, мы начали использовать карданные валы от поставщика из Китая», — сообщил Дмитрий Теплов.
Он полагает, что единственной эффективной программой поддержки сегодня остаются займы от Фонда развития промышленности на приобретение оборудования для производства компонентов.
По словам Теплова, КРМЗ успел воспользоваться программой промышленной ипотеки — для строительства нового цеха по производству сельхозтехники. Инвестиции составили около 100 млн рублей, проект стартовал осенью 2023 года, основная часть строительства велась летом 2024 года. «Но сейчас, при текущей ключевой ставке, промышленная ипотека неподъёмна для большинства производителей», — констатирует директор КРМЗ.
В свою очередь, коммерческий директор «РД Групп» Сергей Матвеев, напоминая о том, что уровень кредитных ставок сейчас составляет 25% и более, рассказал, что с мая по сентябрь 2024 года компания пыталась с двумя крупными российскими банками пройти процесс оформления промышленной ипотеки, но успеха не достигла. Сначала им отвечали, что «есть постановление, но нет лимитов», потом средства появились, но для «РД Групп» кратно увеличили процентную ставку, и компания вынуждена была отказаться. В результате строительство нового завода заморозили.
«Безусловно, разработка — важный и ёмкий человеческий ресурс, но он приносит эффект, когда создаваемый продукт своевременно может быть внедрён в серийное производство, для чего требуется оборудование и площади. Поэтому необходима компенсация затрат производителей и разработчиков. Однако пока мы эффективных мер в данном направлении не видим», — отмечает Сергей Матвеев.
В свою очередь, Дмитрий Теплов обращает внимание на очень жёсткие условия программы. С одной стороны, существуют субсидии на проведение НИОКР, говорит он, но при этом есть обязательства по итоговому производству и реализации определённого объёма компонентов, а он может оказаться не востребован рынком, что в итоге принесёт производителю штрафы. «Такое уже происходило, поэтому потенциальные производители компонентов опасаются вступать в программу субсидирования НИОКР», — объясняет Теплов.
В этой связи Сергей Матвеев упомянул, что у компании есть три законченных НИОКР в рамках постановления правительства №1649, но в серию пока запущен только один продукт — система контроля давления и температуры в шинах. Два других продукта — датчики содержания кислорода (О2) и оксидов азота (NOx) в выхлопных газах — потребитель предпочитает пока покупать у китайских производителей, а отечественные не могут приблизиться к их цене, признаёт Матвеев.
Тем не менее, определённые положительные шаги есть: например, требования использовать российские компоненты в рамках постановления правительства №719, требования СТ-1. По мнению Матвеева, необходима жёсткая протекционистская политика государства, направленная на ограничение ввоза импортных товаров и поддержку производства аналогичных изделий внутри страны. «Никогда мы не получим китайский уровень цен в России. Этому есть целый комплекс причин: в Китае современные технологии обработки, высокая степень автоматизации производства, все материалы логистически доступны в рамках промзоны, электронные компоненты собственного производства, дешёвая электроэнергия, низкая аренда (от 3 USD/кв. м), низкие кредитные ставки (2% годовых). Сравните с нашими условиями!», — негодует коммерческий директор «РД Групп».
Если в поставке комплектующих Китай выступает нашим партнёром, то на рынке готовой продукции он жесточайший конкурент, поддерживает коллег технический директор KOBLiK GROUP Роман Карпенко.
По его словам, китайская промышленность продемонстрировала впечатляющие успехи в освоении технологий производства сельскохозяйственного оборудования. «Китайцы мастерски освоили реинжиниринг европейских образцов. Цепочка кооперации у них развита настолько, что позволяет оставлять у производителя только ключевые производственные процессы, уделяя большее внимание улучшению конечного продукта», — делится наблюдениями Роман Карпенко.
Вместе с тем, отмечает он, конкуренция по стоимости китайской техники и российских аналогов складывается не в нашу пользу: стоимость металла в Китае в два раза ниже, чем в России, государство выделяет до 40% субсидий на экспорт, ставки по кредитам составляют 4-5% годовых.
То есть, продолжает Карпенко, китайские производители располагают программами поддержки и финансовыми ресурсами, не сопоставимыми с российскими, которые либо отсутствуют, либо не всегда доступны. «Например, при текущей ключевой ставке и снижении покупательской способности можно смело предположить, что любые масштабные инвестиции производители будут откладывать», — заключает специалист.
При этом он подчёркивает: решение проблем отечественного машиностроения — задача многолетняя и требует координированных действий государства, бизнеса и научного сообщества.
В свою очередь, генеральный директор United Industrial (ранее CNH Industrial Russia) Михаил Мураховский наиболее эффективными мерами поддержки считает долгосрочные проекты по субсидированию отрасли в целом и стимулированию спроса на отечественные решения со стороны сельхозпроизводителей. «Только при стабильном спросе возникает возможность планируемого развития и внедрения новых решений для сельского хозяйства», — уверяет он.
Кроме того, среди существующих мер поддержки Михаил Мураховский выделяет предоставление грантов на исследования для специализированных учреждений. Также, по его словам, существуют возможности получения компенсаций за проведённые работы в области реверс-инжиниринга. Схемы поддержки фундаментальных и целевых исследований, как объясняет Мураховский, осуществляются в рамках специализированного постановления правительства, а также целевой помощи от министерств. Для коммерческих же инжиниринговых компаний действуют субсидии инновационного развития от фонда «Сколково».
В первом случае, по его словам, задача и исполнение идёт от аккредитованных научно-исследовательских объединений. Сроки и бюджеты значительны. Второй вариант ориентирован на коммерческие структуры и на более быстрый и конкретный результат.
«Мы как компания видим потенциальную пользу во втором варианте. Но отсутствие прозрачности поддержки и применение исключительно информационных платформ для коммуникации затрудняют процесс. Нет возможности оперативной консультации по возникающим вопросам, нет уверенности, что процесс подачи документов выполняется корректно», — делится Михаил Мураховский.
Несмотря на это, добавляет специалист, компания рассчитывает на получение поддержки от фонда «Сколково», поскольку её предложение позволит расширить перечень инновационных проектов.
Как вспоминает Дмитрий Теплов, стимулирование процессов реинжиниринга началось в России ещё в 2014 году. Уже тогда начали активно продвигать тему импортозамещения. Была создана система региональных центров реинжиниринга, которые выясняют запросы местных предприятий, а затем подключают к решению проблемы научные организации, лаборатории и технологические базы профильных вузов.
КРМЗ тоже неоднократно использовал возможности научно-технологических университетов Пермского края, в частности, их технологии 3D-сканирования.
«Трудности начинаются, когда новый узел готов к производству и нужно выходить с ним на большой российский рынок, встраиваться в действующие технологические цепочки. Государство здесь должно помогать небольшим производственным компаниям продвигать свои компоненты и технологии, а для этого нужна огромная работа, включающая проведение выставок, семинаров, создание системы обмена знаниями», — считает Дмитрий Теплов.
В сфере АПК одним из решений, по его мнению, могли бы стать образцовые фермы, на которых работают российские машины.
«Кстати, независимые конструкторские бюро и их квалифицированные сотрудники могут быть поддержаны государством по аналогии с IT-компаниями: налоговыми льготами, системой льготной ипотеки. Это стимулировало бы приток новых идей и решений», — не сомневается Теплов.
Сами производители, продолжает он, тоже могут способствовать продвижению российских решений. Так, директор КРМЗ рассказал, что «Деловая Россия» недавно организовала федеральный подкомитет по реинжинирингу. Он начал свою работу в рамках комитета по машиностроению. Руководителем стал Алексей Шардин — директор «Волго-Камской инжиниринговой компании», член генерального совета «Деловой России» и член Регионального Совета пермского отделения.
Цель подкомитета, как сообщил Дмитрий Теплов, - консолидация опыта и компетенций в сфере реверс-инжиниринга, ускорение процессов импортозамещения. Подкомитет займётся созданием реестра компаний-членов «Деловой России», приобретающих запчасти, инструменты и принадлежности за рубежом и реестра компаний, специализирующихся в области реверс-инжиниринга ЗИП и реинжиниринга оборудования. Также будет создан реестр компаний, которые могут обеспечить трансфер технологий, адаптируя свои производственные линии под потребности внутренних заказчиков.
С точки зрения председателя правления Ассоциации дилеров сельскохозяйственной техники «АСХОД» Александра Алтынова, в России, прежде всего, надо возрождать экспертизу разработчиков и технологов, а также менять подходы в целом. «Нужно не бояться отвечать на смелые вызовы и решать сложные вопросы, не оглядываясь исключительно на государство. Это долгий и сложный процесс, но пока он не наберёт темпы, не будет и выраженных результатов», — уверен Алтынов.
Отдельной проблемой эксперт называет станкостроение, в котором наше отставание огромно. «Изменение ситуации — задача на пару десятков лет и, конечно, государство должно иметь чёткую стратегию по её реализации», — говорит Алтынов.
В свою очередь, генеральный директор «Грязинского культиваторного завода» Александр Исаков одной из ключевых проблем отрасли считает дефицит отечественных комплектующих, необходимых для производства высокотехнологичной сельскохозяйственной техники. По его данным, особенно остро стоит вопрос нехватки электронных систем управления, широкой номенклатуры колёс и колёсных дисков, высокопрочных специализированных метизов. «Создание их отечественных аналогов требует значительных инвестиций, длительных разработок и устойчивого спроса, которого пока недостаточно. В результате предприятия вынуждены либо закупать критически важные узлы за рубежом, либо упрощать конструкцию машин, что негативно сказывается на технологичности и эффективности оборудования», — констатирует Исаков.
Вслед за Александром Алтыновым он также указывает на отсутствие некоторых видов современных отечественных станков, необходимых для высокоточного производства. Из-за этого, объясняет Александр Исаков, у нас вынужденная зависимость от импорта, высокая стоимость закупки и обслуживания иностранных станков, а также отсутствие надёжной технической поддержки на территории России, что значительно замедляет развитие производственных процессов и увеличивает затраты предприятий. В результате производительность труда не растёт, а себестоимость продукции возрастает, что напрямую влияет на конкурентоспособность российской техники на внутреннем и внешнем рынках.
Высокая себестоимость производства в условиях дефицита инженерных кадров, говорит Исаков, является серьёзным ограничением для развития отрасли. Российские предприятия, реализуя стратегию импортозамещения, стремятся достичь уровня технологического развития ведущих европейских и американских производителей. Однако при этом они вынуждены сохранять конкурентоспособную цену, что существенно ограничивает их возможности для долгосрочного развития. В результате рентабельность российских производителей остаётся недостаточной для масштабных инвестиций в качественные НИОКР, продвижение продукции на рынке, а также создание эффективной системы сервисной поддержки. При этом последние факторы являются важным конкурентным преимуществом зарубежных компаний, к уровню обслуживания которых уже привыкли потребители.
Генеральный директор Грязинского культиваторного завода уверен: для стимулирования технологической независимости и повышения конкурентоспособности отрасли необходимы специализированные дополнительные меры государственной поддержки, которые станут катализатором роста для современных и развивающихся предприятий. В первую очередь, подчёркивает он, важно внедрить программы поддержки цифровизации и роботизации промышленных предприятий. «Эти инициативы позволят не только снизить себестоимость отечественного оборудования, но и вывести российское сельхозмашиностроение на новый уровень технологического развития», — заключает Александр Исаков.