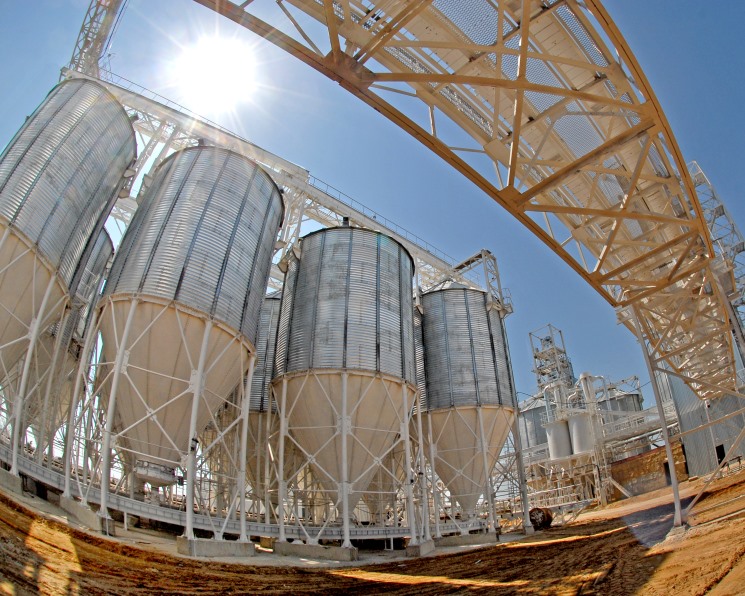
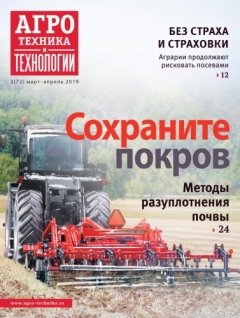
Журнал «Агротехника и технологии»
В России не первый год наблюдается недостаток мощностей для хранения зерна. Большинство имеющихся элеваторов и складов напольного хранения было возведено более 30 лет назад, и сегодня они представляют собой предприятия с высоким уровнем затрат, не всегда обеспечивающие сохранность зерна. Физический износ их основных фондов составляет в среднем 70%. Возведение новых мощностей ведется, но в слишком медленном темпе
Кто может себе позволить строительство современного элеватора и какие требования предъявляют аграрии к оборудованию для хранения и подработки зерна, разбирался корреспондент журнала «Агротехника и технологии».
Основная проблема заключается не в общей нехватке мощностей для хранения зерна, а в недостатке современных предприятий зернохранения, отвечающих требованиям сегодняшнего дня, отмечает Дмитрий Корнев, руководитель отдела зерновой логистики московского представительства Bühler AG (разработка и поставка технологий и оборудования для сельского хозяйства). «Урожай 2017 года подтвердил, что в стране существуют мощности для размещения около 130 млн т зерна. Однако из этого количества соответствуют современным требованиям мощности для хранения не более 35 млн т», — приводит данные специалист.
«Рекордный валовый сбор зерна в 2017 году, а также немаленький урожай 2018-го в очередной раз показали проблему нехватки элеваторных мощностей для его хранения», — подтверждает Юрий Гридчин, начальник отдела маркетинга, комплектации и сбыта Корпорации «СКЭСС» (строительство элеваторов). По его оценке, на сегодняшний день в среднем по стране дефицит емкостей для хранения зерна составляет примерно 20 млн т.
Как рассказал Юрий Гридчин, из-за отсутствия высокотехнологичных современных элеваторных комплексов аграриям приходится размещать свой урожай в складах и под навесами. Отсюда — ухудшение качества зерна и его потери. Соответственно, возникает потребность в строительстве высокотехнологичных элеваторов, способных принять, переработать и сохранить урожай.
«По разным оценкам, негде хранить от 10 до 20 млн т зерна», — приводит данные Алексей Смарагдов, директор по развитию Группы компаний Baitek Machinery (поставка спецтехники ведущих европейских производителей). Кроме того, добавляет он, большинство коммерческих элеваторов, построенных еще в Советском Союзе, нуждаются в реновации. Специалист обращает внимание, что особенно остро стоит вопрос о модернизации и закупке зерносушилок. Дело в том, что климатические условия в России предполагают сушку большинства сельскохозяйственных культур, особенно масличных, доля которых в валовом урожае неуклонно растет. Без надлежащей сушки зерно невозможно хранить долгое время без потери его качеств. Кроме того, влажный ворох имеет тенденцию к самосогреванию и, в конечном итоге, порче.
Ссылаясь на данные ФТС России, Алексей Смарагдов отмечает, что в среднем в год в страну поставляется около 200 зерносушилок импортного производства. Около 450 агрегатов поставляют отечественные производители. «Но даже при таких высоких объемах рынок далеко не насыщен, — подчеркивает он. — Это связано в том числе с тем, что большинство сельхозтоваропроизводителей — от крупных агрохолдингов до фермерских хозяйств, занятых в растениеводстве, — предпочитают инвестировать в собственные элеваторы, способные обеспечить качественную подработку, сушку и хранение урожая. Экономически это более выгодно, чем пользоваться услугами коммерческих элеваторов».
Юрий Гридчин приводит статистику, согласно которой за последние 5 лет в России введены в эксплуатацию современные зернохранилища объемом хранения около 3 млн т, что, по его мнению, крайне мало, учитывая дефицит элеваторных мощностей.
А вот по оценкам компании Bühler AG, каждый год в стране вводятся в эксплуатацию элеваторные мощности для хранения 1,5-2 млн т, при этом ежегодно выводятся из оборота устаревшие склады объемом хранения около 0,5-0,8 млн т. «Заказчиками нового строительства выступают как крупные агрохолдинги, стремящиеся полностью контролировать сырьевую логистику, так и агрофирмы регионального масштаба, которые достигли зернового оборота около 100 тыс. т в год и не хотят зависеть от местных элеваторов», — говорит Дмитрий Корнев.
По наблюдениям же Юрия Гридчина, основными заказчиками в настоящее время являются крупные агрохолдинги, в основном производители молока и мяса, а также компании, занимающиеся экспортом зерновых, которые заинтересованы в строительстве портовых терминалов.
Владимир Матлахов, заместитель генерального директора — директор по свиноводству и кормопроизводству ГК «Агро-Белогорье» (промышленное свиноводство и мясопереработка, молочное животноводство, растениеводство и кормопроизводство)
«Комбикормовые заводы ГК «Агро-Белогорье» имеют суммарную единовременную мощность хранения зерна 273 тыс. т. Из них на металлосборные зернохранилища приходится 147 тыс. т, а на склады напольного хранения — 126 тыс. т. Также имеются три металлосборных элеватора на трех комбикормовых заводах холдинга. Яковлевский комбикормовый завод располагает 20 емкостями суммарной мощностью хранения 60 тыс. т, Ливенский комбикормовый завод — 20 емкостями общей мощностью 30 тыс. т, Новоборисовское ХПП располагает 23 емкостями, рассчитанными на хранение 57 тыс. т зерна. При этом на базе Ливенского комбикормового завода существует дефицит мощностей, который составляет около 30 тыс. т. В настоящее время обсуждается возможность расширения элеваторных мощностей».
Что выбирают аграрии?
По словам Алексея Смарагдова, рынок оборудования для хранения и подработки зерна показывает устойчивый рост последние 10 лет. Это обусловлено рядом факторов. «Во-первых, происходящим в последнее время укрупнением хозяйств. Многие фермеры и небольшие сельскохозяйственные кооперативы не выдерживают конкуренции с агрохолдингами, которые имеют полный цикл производства продукции и выход на экспортные рынки, а также на прилавки крупных ритейлеров, — объясняет специалист. — Агрохолдинги более устойчивы в финансовом плане и застрахованы от волатильности рынка. Им легче пережить неурожайный год. Крупные хозяйства предпочитают сами подрабатывать и хранить зерно, изготавливать семена, сокращая тем самым производственные издержки».
Во-вторых, продолжает Алексей Смарагдов, играет свою роль экономический фактор. Традиционно самая низкая цена на урожай приходится на уборочную страду, самая высокая — на весну. Обладая собственными мощностями для хранения, аграрии могут «придержать» зерно и реализовать его по наиболее выгодной цене. В-третьих, отмечает он, это уже упомянутое моральное устаревание оборудования.
В целом, по мнению директора по развитию ГК Baitek Machinery, компании, нуждающиеся в элеваторных мощностях, можно разделить на условные группы, исходя в первую очередь из площади посевов. Данное деление достаточно условно, но в целом отражает картину по стране. «К первой группе относятся хозяйства с площадью посевов до 2 тыс. га, — говорит он. — Такие аграрии, чаще всего это КФХ, выбирают классические ЗАВы, оснащенные машинами для очистки зерна, транспортными бункерами и зерносушилкой, как правило, мобильной».
Самый широкий ряд мобильных зерносушилок представлен у итальянской компании Fratelli Pedrotti, считает Смарагдов, подчеркивая, что производительность данных агрегатов находится в диапазоне от 55 до 450 т в сутки.
«Хранение на таких предприятиях чаще всего напольное, то есть в кирпичных или металлических бескаркасных ангарах, — добавляет он. — Такое решение привлекает прежде всего низкими начальными инвестициями, отсутствием необходимости получать специальные разрешения на строительство и быстрой окупаемостью».
Вторая группа, по словам Алексея Смарагдова, представлена хозяйствами с общим земельным банком до 30 тыс. га. Эта группа предпочитает устанавливать автоматизированные линии по приемке, очистке и сушке зерна, рассчитанные на большие объемы переработки и интенсивную круглосуточную работу. «В такие комплексы устанавливаются стационарные зерносушилки поточного типа отечественного или импортного производства, — объясняет он. — Как правило, производительность комплексов достигает 100 т в час. Для хранения урожая используются как напольные ангары, так и вертикальные металлические силосы. Обычно емкости для хранения также автоматизированы: оснащены системами вентиляции и телеметрии».
Третья группа включает в себя агрохолдинги с площадью пашни свыше 30 тыс. га, коммерческие элеваторы, хлебоприемные предприятия, продолжает директор по развитию ГК Baitek Machinery. Для элеваторов данной группы характерны полная автоматизация, большие объемы хранения (от 10 до 100 тыс. т и более), а также значительные инвестиции. Как правило, крупные холдинги отдают предпочтение элеваторам импортного производства с высокопроизводительными энергосберегающими зерносушилками.
«Потребности у предприятий самые разные. Одним требуется многократное заполнение и опорожнение емкостей. Другим — заполнение единожды во время закладывания собственного урожая после уборки или хранения закупленного для дальнейшей переработки/продажи зерна», — делится наблюдениями Армен Налбандян, генеральный директор компании «Лилиани» (российский разработчик решений по оптимизации логистики уборки, сева и хранения зерновых). Но одно требование для всех общее — обеспечение качественного хранения при возможном минимуме инвестиций и операционных затрат, подчеркивает он.
Расходы на сушку и хранение 1 т продовольственной пшеницы III класса на коммерческом элеваторе в октябре 2018 года составляли 1197,48 руб., а на собственном комплексе — всего 166,98 руб. Стоимость строительства элеватора составляет в среднем 12-15 тыс. руб. за тонну, а срок его окупаемости — 5-7 лет
Эффективность в приоритете
Директор по управлению цепями поставок Группы «ПРОДО» Генрих Арутюнов оценивает эффективность элеватора по совокупности двух ключевых факторов: современные технологии и коммерческая оборачиваемость. «Проще говоря, технологии должны обеспечить получение продукта с требуемыми показателями за минимальное количество повторяемых операций. А коммерческая эффективность элеватора должна быть не менее 2,5-3 оборотов элеватора за сезон (речь не идет о портовых элеваторах)», — считает специалист.
«Сейчас рынок предлагает широкий выбор элеваторного оборудования. Так, наиболее востребованы проекты элеваторов с металлическими силосами, причем отечественные и зарубежные производители предлагают стандартные проекты в любой комплектации», — говорит Дмитрий Корнев. Он подчеркивает, что современные технологии обеспечивают таким элеваторам преимущество против бетонных элеваторов старых конструкций (постройки 1960-1980-х годов): по удельной энергоемкости — в 1,5 раза, по удельной материалоемкости — в 1,3-1,5 раза, по уровню автоматизации — в 2-3 раза.
Кроме того, по словам специалиста, технологические процессы с зерном на современных элеваторах требуют затрат в 1,5-2 раза меньше, чем те же процессы на элеваторах старых конструкций. Кроме того, штат сотрудников также сокращается в 2-3 раза. «В настоящее время в России число занятых на производстве людей на многих новых элеваторах не превышает этот показатель на элеваторах США и Западной Европы», — обращает внимание Дмитрий Корнев.
Владимир Матлахов, заместитель генерального директора — директор по свиноводству и кормопроизводству ГК «Агро-Белогорье», уверяет, что элеваторы их агрохолдинга соответствуют статусу «высокоэффективный зерновой элеватор». Они оборудованы приемными отделениями с автоподъемниками, зерноочистительным оборудованием, высокоэффективными сушилками зерна, транспортным оборудованием загрузки и выгрузки зерна, системами вентиляции для ухода за зерном на хранении, системами контроля температуры и системами дистанционного управления оборудования АСУТП, перечисляет специалист. По его словам, на элеваторах установлено оборудование российских и европейских производителей, таких как «СКЭСС», Symaga Group, BDW, Bühler, FAW, FAO.
«Зерно хранится в состоянии пониженной влажности (ниже критической). Качество зерна, принимаемого и отгружаемого с хранения, соответствует ГОСТам на хранимые культуры. Потери при хранении находятся в пределах норм естественной убыли от дыхания зерна», — уточняет Владимир Матлахов.
«Высокоэффективный элеватор — это предприятие, способное как принимать, так и отпускать зерно в любой вид транспорта, а также подрабатывать сырье любого качества, доводить его до кондиции и хранить продолжительное время без потерь основных потребительских характеристик», — убежден Валерий Малыгин, директор Лузинского комбикормового завода (входит в Группу «ПРОДО»). Он рассказал, что элеватор Лузинского комбикормового завода был введен в эксплуатацию в 1987 году. С момента запуска используется только отечественное оборудование, которое исправно работает на протяжении 30 лет.
«Наш элеватор, в отличие от линейного, изначально был спроектирован в комплексе и под потребности комбикормового завода, — объясняет Валерий Малыгин. — Мы работаем в цепочке: от приемки кондиционного зерна собственного производства и его частичной подработки (очистки от примесей и сушки) до хранения и производства комбикормов. Текущая производственная мощность завода — 750 т кормов в сутки».
Очистка и сушка зерна, по его словам, производится на отечественном оборудовании. Для очистки используются машины А1-БИС-100 и С-1500, для сушки — Р1-СЗГ серии ASTRA. После подработки зерно укладывается на хранение и, по мере необходимости, передается в цех комбикормового производства. Если говорить о потерях при хранении, то они, по заверению директора Лузинского комбикормового завода, соответствуют нормативам. При допустимой норме в 1 % (это технические потери, сорность и так далее) потери минимальны — 0,56 % и ниже.
«Высокоэффективные зерновые элеваторы в наше время должны быть оснащены блок-схемами с высокопроизводительным оборудованием (очистительные машины, зерносушилки, нории и транспортеры)», — убежден Максим Курочкин, директор элеватора Группы компаний «АгроТерра» (один из лидеров отрасли растениеводства; объединяет в партнерскую сеть соседствующих средних и мелких агропроизводителей). Именно это, по его мнению, позволяет доводить зерно до базисных норм качества по международным стандартам и совершать несколько оборотов перевалки за сезон при наименьших трудозатратах.
«На таких элеваторах можно производить до 10 операций одновременно. В результате становится возможной бесперебойная круглосуточная работа по приемке и отгрузке продукции автомобильным и железнодорожным транспортом», — подчеркивает Максим Курочкин. Кстати, в компании «АгроТерра» сохранность продукции обеспечивают 20 современных элеваторов общей мощностью более 500 тыс. т.
Генрих Арутюнов, директор по управлению цепями поставок Группы «ПРОДО» (растениеводство, производство кормов, свиноводство, птицеводство, мясопереработка, молочное производство
«На каждом предприятии Группы «ПРОДО» есть оперативные мощности по вертикальному хранению зерна, которые позволяют создавать трехмесячный запас. Профессиональный элеватор один — на Лузинском комбикормовом заводе в Омской области. При создании значимых сезонных зерновых запасов приходится прибегать к услугам сторонних элеваторов. На сегодняшний день мы ощущаем нехватку мощностей и рассматриваем элеваторные активы для приобретения. Эта проблема есть по всей стране, так как резко вырос валовый сбор зерна за последние годы, а элеваторные мощности строятся и обновляются низкими темпами, устаревают и выходят из строя советские элеваторы. В результате мы имеем рост цен на услуги элеваторов и дефицит мощностей по хранению зерна».
Автоматизация и качество зерна
К современным элеваторам предъявляются повышенные требования по эффективности, автоматизации и безопасности. Бесперебойная работа элеватора, особенно в периоды пиковых нагрузок, обеспечивает полную сохранность собранного урожая, утверждает Алексей Смарагдов.
Он объясняет, что основное требование к высокотехнологичному комплексу по переработке и хранению зерна — полная автоматизация всех рабочих процессов. В идеале один или два оператора должны контролировать все процессы на элеваторе: приемку зерна, его очистку и сушку, закладку на хранение, отгрузку на автомобильный или железнодорожный транспорт. Технологическая схема элеватора должна предполагать различные варианты движения зернового потока в зависимости от конкретных условий: влажности, засоренности. Расположение оборудования должно быть эргономичным, удобным для периодического обслуживания и инспектирования, иметь удобные подъездные пути. Очень важно соответствие нормам промышленной и экологической безопасности, ведь только штрафы за нарушение природоохранных норм могут достигать десятков миллионов рублей. Особенно если объект расположен в черте города.
«Каждый элемент комплекса должен соответствовать расчетной производительности. Ущерб от простоев элеватора — основной фактор снижения эффективности и экономической целесообразности», — указывает директор по развитию ГК Baitek Machinery. По его словам, при проектировании элеватора крайне важно определить не только производительность оборудования, включенного в комплекс, но и общее состояние хозяйства. Потребность в мощностях для хранения и переработки определяется, исходя из общего объема для хранения, потребности в сушке зерна, состояния комбайнового парка и возможностей транспортной логистики. Если упустить из виду хотя бы один из факторов, убытки неизбежны, предупреждает специалист.
Как рассказал Алексей Смарагдов, особые требования предъявляются к зерносушильному оборудованию, так как это ключевой элемент всего комплекса. Использование зерносушилки наиболее затратно, а стоимость сушки напрямую влияет на себестоимость конечного продукта. Основные требования, предъявляемые к зерносушилке: пожарная безопасность, соответствие заявленной производительности реальным условиям работы, экономия электроэнергии и топлива, высокое качество зернового материала на выходе, возможность эффективной работы при любых климатических условиях. «Последнее особенно важно для России, где сушка некоторых сельскохозяйственных культур (кукурузы, подсолнечника) происходит поздней осенью или даже зимой», — обращает внимание он.
Серьезные требования по безопасности и автоматизации предъявляются также к емкостям для хранения. Алексей Смарагдов объяснил, что они должны быть оснащены системой активной вентиляции и термометрией. Вентиляция помогает поддерживать постоянный уровень влажности зерна и микроклимат внутри силоса. А термометрия обнаруживает очаги согревания, что может быть показателем наличия вредителей или болезнетворных организмов, а также порчи вороха. «Нет нужды упоминать, что загрузка и выгрузка силосов должна происходить автоматически, — отмечает он. — Датчики объема силоса также помогают оператору равномерно использовать емкости для хранения. Крайне важно, чтобы силосы были изготовлены с учетом сейсмической, ветровой и снеговой нагрузок региона, где они будут установлены».
В целом аграрии сходятся во мнении: эффективный элеватор — это элеватор, который, в первую очередь, обеспечивает качество хранения зерна. Поступающее зерно элеватор должен принять, при необходимости произвести его очистку до стандартных кондиций и сушку, если зерно влажное, а затем — заложить на хранение. И хранить это зерно подконтрольно, то есть проверяя температуру нахождения в силосах.
Специалисты подчеркивают, что главное требование, естественно, — возможность элеватора обеспечить хранение зерна длительный период времени без дополнительных затрат. Безусловно, многое здесь зависит от самих силосов, от оборудования, которое установлено на элеваторе. Так, силосы должны быть герметичными, чтобы туда не попадали осадки. Кроме того, они должны быть оснащены термоподвесками для контроля температуры, современной системой вентиляции.
Также аграрии обращают внимание, что любой элеватор не застрахован от зараженности вредителями хлебных злаков, которые попадают с зерном с поля. От урожая к урожаю вредители могут накапливаться в разных стыках, щелях и соединениях. Поэтому, чтобы обеспечить качество зерна, необходимо следить за состоянием силосов, вовремя проводить обработку, газацию.
Кроме того, по их мнению, важен человеческий фактор. Должна быть лаборатория, которая контролирует зерно на всех этапах: при поступлении, очистке, сушке. За каждый этап должен отвечать свой специалист. Без человека железо остается всего лишь железом, напоминают аграрии.
Валерий Малыгин, директор Лузинского комбикормового завода (входит в Группу «ПРОДО»)
«Наш элеватор состоит из 185 железобетонных силосов. Общая емкость единовременного хранения зерновых — 30 тыс. т. В аренду сторонним хозяйствам мощности не сдаются, т. к. в год комбикормовому заводу требуется 120 тыс. т».
Окупятся ли инвестиции?
Строительство нового элеватора — процесс дорогостоящий. Согласно подсчетам Юрия Гридчина из корпорации «СКЭСС», в среднем стоимость строительства элеватора составляет 12-15 тыс. руб. за тонну, а срок его окупаемости — 5-7 лет. А по оценке Дмитрия Корнева, инвестиции на тонну хранения составят € 200-250, и это только прямые затраты. Срок окупаемости достигает 8-12 лет, в зависимости от загруженности (грузооборота) нового объекта.
«Обычно выбор покупателя определяется его бюджетом — при наличии внушительных сумм выбирается проект ведущих производителей. При более скромных средствах нередко покупатели реализуют так называемые сборные проекты, когда оборудование для основных производственных участков приобретается у импортных производителей, а вспомогательное оборудование — более бюджетное», — поясняет специалист компании Bühler AG.
«Строительство элеватора — это затратный процесс, требующий вложений в проектно-изыскательные работы, оборудование, автоматизацию, монтаж и обучение персонала. Как правило, строительство с нуля занимает до трех лет при достаточном объеме инвестиций», — говорит Алексей Смарагдов. Он уверяет, что среднюю стоимость элеватора определить сложно, так как на цену влияет слишком много факторов. Как правило, каждый элеватор — это индивидуальное технологическое решение, учитывающее потребности конкретного хозяйства.
В качестве примера специалист предлагает обратиться к наиболее дорогостоящему в комплексе элементу оборудования — зерносушилке. «Современная энергосберегающая зерносушилка, позволяющая минимизировать затраты на сушку, не будет дешевым удовольствием, — предупреждает он. — Так, стоимость зерносушилки премиум-класса Strahl (Италия) производительностью 50 т в час составит около 17 млн руб.». Правда, оговаривается Алексей Смарагдов, речь идет о полной комплектации: с системой рекуперации тепла, теплоизоляцией шахты, системой пылеподавления, автоматизацией и прочими базовыми опциями. Также он приводит расчеты экономистов, согласно которым расходы на сушку и хранение 1 т продовольственной пшеницы III класса на коммерческом элеваторе составляют на октябрь 2018 года 1197,48 руб., а на собственном комплексе — всего 166,98 руб. Разница — в 7 раз.
При этом, обращает внимание Смарагдов, в расчетах не учитывались расходы на транспортную логистику: доставку зерна на элеватор и его отгрузку при реализации. В довершение картины директор по развитию ГК Baitek Machinery приводит еще один пример. «Владелец СХП “Олимп Агро” Николай Алексеевич Леонтьев является одним из самых успешных аграриев Самарской области по версии ежемесячного издания “Дело”. В 2013 году компания построила производственную базу с площадями для хранения и оборудованием для очистки и сушки зерна Strahl производительностью 110 т в час. После этого в 2014 году выручка выросла в 2 раза и с тех пор увеличивается на 5-15 % в год», — рассказал Алексей Смарагдов. При этом, если не брать в расчеты агрохолдинги, «Олимп Агро» находится на втором месте по показателю чистой прибыли среди аграрных компаний региона.
Таким образом, заключает Смарагдов, мы видим, что значительные инвестиции оправдывают себя: снижение затрат на сушку и хранение зерна существенно уменьшает его себестоимость.
Армен Налбандян, генеральный директор компании «Лилиани» (российский разработчик решений по оптимизации логистики уборки, сева и хранения зерновых)
«За последнее десятилетие в России набрала популярность технология хранения зерна в пластиковых рукавах. Это альтернатива складам и элеваторам, обладающая большим списком взаимодополняющих положительных качеств. В их числе — низкие инвестиции и операционные затраты.
Основной принцип такого хранения — «консервация» зерна в герметичной среде, которая создается при плотной набивке в специальный пластиковый рукав. Самые распространенные габариты рукава: диаметр 2,7 м, длина 60 или 75 м, толщина 230 микрон, вместимость 200 или 250 т пшеницы.
Благодаря своим свойствам рукава обеспечивают полную защиту от влаги, снега и ультрафиолета. Отсутствие воздухообмена с внешней средой способствует концентрации внутри рукава углекислого газа — продукта «дыхания» зерна, а также насекомых и микроорганизмов, попадающих в рукав вместе с ним. А углекислый газ, генерируемый таким естественным образом, являясь природным консервантом, обеспечивает идеальную сохранность зерна.
Высокая производительность системы по закладке в рукава и выгрузке из них также выгодно отличает технологию. Так, средняя дневная производительность загрузки или выгрузки зерна, из расчета на комплект оборудования, составляет 1 тыс. т зерновых. Для загрузки рукава используется зерноупаковочная машина, обеспечивающая подачу зерна в рукав и одновременно полное его набивание. Рукав поставляется в гофрированном виде в больших картонных коробках. После распаковывания его надевают с помощью специального подъемного механизма на тоннель зерноупаковочной машины, вытягивают примерно 3 метра со свободного конца, плотно его закрывают. Потом с помощью шнековый системы машины набивают рукав зерном. При этом машина по мере заполнения рукава «отталкивается» от нее за счет давления, которое оказывает новая порция зерна, подаваемого в наполненный отрезок рукава. Высвобождается новый виток сложенной на тоннель машины пленки, которая сразу же наполняется поступающим зерном. И так до полного заполнения. Когда до конца остается 3-4 метра, остаток пустого рукава снимается с машины и плотно закрывается. Главное — не образовать внутри рукава «карманов» с воздушными пузырьками.
Для подачи зерна в зерноупаковочную машину выбирают либо бункер-перегрузчик, либо автоперегрузчик. Первый вариант интересен в случае одновременной организации весового контроля через встроенную систему взвешивания бункера при подаче из-под комбайнов или из зернотока. А второй вариант более удобен при необходимости подачи в рукав зерна с автомашин прямо с поля. Также этот способ предпочтителен, если грунт, на который укладывается рукав, влажный, что требует низкого давления в шинах,т. е. подача автомашин может быть невозможна.
Для выгрузки применяется специальная машина, которая разгружает зерно прямо из рукава, разрезая его и наматывая выгруженный участок на специальный намотчик-трубу. Такая машина в состоянии выгружать зерно в любую погоду: хоть в дождь, хоть в снег, хоть из-под снега. Если рукава уложены не на бетонную или асфальтовую поверхность, а на обычное поле, то вывоз зерна из рукава (поля) в любой сезон можно производить с помощью бункеров-перегрузчиков с дальнейшей перегрузкой в автомашины».