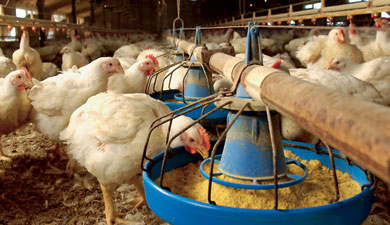
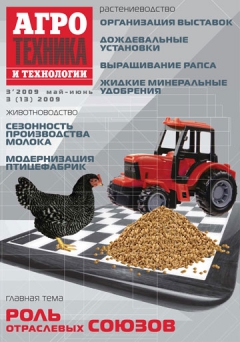
Журнал «Агротехника и технологии»
По данным экспертов, сегодня около 320 российских птицефабрик находятся в состоянии реконструкции. Также в последние годы активизировалось строительство новых площадок в прежде неосвоенных регионах. Такая ситуация сформировалась благодаря государственным инвестициям и жесткой конкуренции на рынке мяса птицы.
Кризис, который существенно затронул птицеводческую отрасль в 1990-е годы, когда низкие пошлины на ввозимую курятину поставили отечественных производителей буквально на грань выживания, был преодолен только в последнее десятилетие. Росптицесоюз разработал отраслевую целевую программу развития птицеводства на 2005-2010 годы, к тому же с 2006 года вступил в силу нацпроект, который также имел для отрасли очень большое значение. В результате у птицеводов появились средства для развития. «За последние годы инвестиции в отрасль составили более 50 млрд руб., — приводит данные президент Росптицесоюза Владимир Фисинин. — Большей частью эти деньги пошли на модернизацию и строительство птицефабрик и использовались в основном для погашения долгосрочных субсидируемых кредитов, которые были предоставлены целому ряду предприятий». «Сегодня многие предприятия, определяющие политику продовольственного рынка в рамках национального проекта «Развития АПК» и первого года реализации Госпрограммы, провели модернизацию, а это вместе с новым строительством позволяет ежегодно увеличивать производство мяса птицы на 15%», — добавляет гендиректор Росптицесоюза Галина Бобылева. Такие высокие показатели прироста обеспечиваются главным образом за счет непрекращающейся реконструкции имеющихся мощностей и лишь на 35-40% поддерживаются благодаря новому строительству, утверждает она, поясняя, что это связано в первую очередь с тем, что модернизировать старые предприятия существенно дешевле, чем строить новые. Эксперт также объясняет, что модернизация — это перманентный, растянутый во времени процесс. «Обновление оборудования идет постоянно, отдельные узлы и линии модернизируются ежегодно. Поэтому даже тем, кто «отремонтировался» совсем недавно, полезно держать руку на пульсе», — советует она.
На полу или в клетке?
Вопрос о способе содержании птицы остается одним из ключевых при модернизации или строительстве новой птицефабрики. «Тенденция внедрения напольного оборудования появилась в 1990-е годы, когда на нас обрушился мощный импорт птицы. Оно дешевле и с учетом сокращения объемов производства вполне устраивало аграриев. Однако съем с единицы площади при напольном содержании значительно меньше, чем при использовании клеток», — подсчитывает Бобылева. «Раньше у клеток были плохие полики, которые давали намины. Дело в том, что кормушки располагались снаружи клеточной батареи, и птице приходилось тянуться, в результате чего она испытывала стресс. Все это, безусловно, сказывалось на качестве производимой продукции, и на фоне этих условий использование напольного оборудования действительно являлось передовой технологией, значительно повышающей комфортность содержания», — вторит Бобылевой Фисинин.
Однако эксперты объясняют, что сегодня ситуация резко изменилась, и клетка стала использоваться гораздо активнее. Это связано в первую очередь с внедрением новых технологий, которые позволили сделать ее значительно комфортнее: полики сегодня изготавливаются из пластика, также появились новые системы ниппельного поения, ленты для уборки помета. Благодаря этому экономическая эффективность выращивания бройлера в клетке в несколько раз выше, чем на полу и в хозяйствах, где напольное оборудование отслужило свой срок, в большинстве случаев идет его замена на клетку. «Сегодня 99% яиц производятся в клеточных батареях, а из 162 бройлерных фабрик клеточное оборудование используется на 47», — приводит статистику Фисинин. Говоря о тенденциях последних нескольких лет, эксперты в один голос отмечают увеличение количества птицефабрик с клеточным содержанием. Это связано преимущественно с довольно жесткой конкуренцией на рынке, которая заставляет использовать площади своего хозяйства максимально эффективно (средний сбор мяса с кв. м на фабрике с напольным содержанием составляет 280-300 кг/год против 600 кг/год при использовании клеточных батарей), объясняет президент Росптицесоюза.
Реконструкция старых сооружений
На оборудовании, которое было установлено в 1970-е годы, сегодня работают единицы, утверждает Виктор Пресняков, генеральный директор компании «Центрптицепром» (Оренбургская область, агрохолдиг). Во-первых, срок его службы давно истек, а во-вторых, в условиях жесткой конкуренции на нем невозможно наладить прибыльное производство, поясняет специалист.
При модернизации происходит полная замена оборудования, говорит Пресняков. «В первую очередь в здании необходимо поменять кровлю и полы, затем установить новое оборудование поения и кормления птицы и наладить систему вентиляции, а также обеспечить обогрев помещений наиболее передовыми способами», — перечисляет он. При ограниченности средств специалист советует сначала поменять оборудование поения и кормления, о вентиляции можно подумать во вторую очередь.
Сергей Карабанов, генеральный директор компании «Баси» (Саратов, консалтинг в сфере птицеводства), считает, что сначала на птицефабриках нужно модернизировать те конструкции, от которых зависит доходность предприятия. Прежде всего это кормоцеха, клеточное оборудование, системы вентиляции, системы отопления, оборудование по переработке птицы.
При этом Карабанов замечает, что при покупке нового оборудования аграрии чаще стали отдавать предпочтение европейским установкам. Это неудивительно, ведь в период застоя отечественная птицеводческая промышленность практически не развивалась, оборудование для нее не производилось, что в конечном итоге привело к техническому отставанию нашего специализированного машиностроения, огорчен специалист.
Одним из примеров проведения модернизации с использованием европейской техники может служить опыт «Центрптицепрома» и двух входящих в него птицефабрик, «Уральский бройлер» и «Оренбургский бройлер». Замена оборудования в племрепродукторе и птицеводческих помещениях этой компании началась в 2003 году и продолжается до сих пор. В результате модернизации объемы производства по сравнению с советским периодом выросли более чем в 2,5 раза, и сегодня здесь ежегодно производят 32,5 тыс. т мяса птицы и 18 млн штук инкубационного яйца. «Мы установили бельгийские агрегаты Roxell для кормления и поения, а также датское вентиляционное оборудование компании Skov и голландские вентиляторы Tulderhof, — рассказывает Пресняков. — В рамках продолжения реконструкции мы ведем активные переговоры с компаниями
Big Dutchman и Hartman (Германия), так как при проведении первичной модернизации нам не хватило средств, и часть агрегатов мы заменить не успели. Однако уже в нынешнем году мы планируем полностью завершить реконструкцию», — надеется специалист.
О коммерческих подробностях реконструкции в хозяйстве Пресняков умолчал, сообщив только, что окупаемость птицеводческих проектов составляет в среднем 5-6 лет. В целом же новым оборудованием в хозяйстве остались довольны. По словам специалиста, оно полностью отвечает технологическим требованиям по выращиванию птицы. «Случались, конечно, незначительные поломки, но они легко устранялись нашими специалистами», — вспоминает Пресняков. По его мнению, основным аргументом в пользу сотрудничества с компаниями
Big Dutchman и Hartman является наличие у них российских представительств и складов на территории нашей страны. «Roxell и Skov не имеют российских представительств, а ждать, пока нам доставят вентилятор из Европы, мы не готовы, именно поэтому было принято решение о прекращении сотрудничества с этими фирмами», — поясняет аграрий.
Примерно по той же схеме происходит модернизация в хозяйстве «Ставропольский бройлер» (Ставрополь, напольное содержание птицы). По словам Михаила Водолазского, директора бизнес-подразделения животноводства, она уже давно приняла плановый непрерывный характер. «При работе с поставщиком оборудования мы прежде всего ориентируемся на соотношение цены и качества, — рассказывает он. — В 2007 году, выбирая напольное оборудование для содержания птицы, мы отдали предпочтение Big Dutchman. Тендер на оборудование для нашего родительского стада (мы скоро будем модернизировать 12 птичников) тоже выиграла эта компания. Но системы автоматического яйцесбора мы планируем покупать у Vencomatic (Голландия)».
Несмотря на верность практически одному и тому же производителю, Водолазский отрицает наличие на рынке оборудования для птицеводческих хозяйств каких-либо ярко выраженных лидеров. «Big Dutchman, конечно, развилась достаточно сильно и может позволить себе делать существенные скидки, которые не отражаются на качестве оборудования, что позволяет ей выигрывать тендеры. Однако уже сейчас мы прицениваемся и к турецкому, и к китайскому оборудованию. Если соотношение цена-качество покажется нам приемлемым, мы с удовольствием пойдем на сотрудничество с азиатскими фирмами, тем более что Турция ближе Дании, и транспортные расходы при доставке оттуда меньше», — делится планами специалист.
Где покупать оборудование?
Наладить производство оборудования для всей технологической цепочки производства птицы (заканчивая убоем и переработкой) внутри одной страны довольно сложно. Это очень трудоемко и, по словам экспертов, не имеет экономического смысла. Поэтому на территории современной России и бывших советских республик нет и никогда не было заводов, выпускающих оборудование для переработки птицы, говорит Фисинин. «Крупнейшие голландские компании Stork и Meyn, а также датская Linсo снабжают таким оборудованием весь мир, включая США и Бразилию, но попытка наладить подобное производство в России ничего, кроме убытков, не принесет», — не сомневается эксперт.
Но при этом Фисинин и ряд других экспертов подчеркивают, что клеточное оборудование для содержания птицы, причем высокого качества, вполне можно покупать и внутри страны. Например, «Пятигорсксельмаш» (Пятигорск, оборудование для птицеводства) освоил все новейшие технологии в деле производства клеточного оборудования и выпускает 3-, 4-, 5-ярусные клетки, говорит президент Росптицесоюза. Также одним из хороших производителей российского оборудования является «Голицынский завод средств автоматизации» (Московская область), где выпускаются клеточные батареи для кур-несушек, ремонтного молодняка и бройлеров, объясняет эксперт.
Замечательным примером использования отечественного оборудования является опыт Рефтинской птицефабрики (Свердловская область). Применяя для содержания птицы клеточные батареи, купленные у «Пятигорсксельмаша», хозяйство производит 25 тыс. т мяса в год, снимая 614 кг мяса с кв. м. Тогда как при напольном выращивании бройлеров съем мяса с 1 кв. м не превышает 300 кг.
Также аргументом в пользу отечественного оборудования является высокий курс доллара, который установился в последнее время. В этой ситуации сотрудничать с российскими производителями стало гораздо выгоднее. Более того, по словам Фисинина, покупатели импортного оборудования сталкиваются с проблемами плохого сервисного обслуживания.
Его мнение подтверждает Сергей Борисов, проект-менеджер компании «Стимул Инк» (Московская область), занимающейся реконструкцией птицефабрик. Специалист рассказывает, что при работе с заказчиками он все чаще слышит пожелания использовать для оснащения птицефабрик отечественное оборудование, хотя, по его утверждению, это связано в первую очередь с экономическим кризисом, ростом курса валют и удорожанием импортного оборудования.
Однако не все специалисты лояльны к отечественному производителю. Так, Пресняков из «Центрптицепрома» объясняет, что из российских предприятий только «Пятигорсксельмаш» выпускает оборудование для клеточного содержания птицы, но его качество оставляет желать лучшего. «Технологически это оборудование еще далеко от совершенства, оно не соответствует современным требованиям», — утверждает специалист. Пресняков отдельно подчеркивает, что на свою продукцию «Пятигорсксельмаш» устанавливает неадекватно высокие цены. «В такой ситуации приходится сотрудничать с западными компаниями, что особенно неприятно в связи с экономическим кризисом и изменением курса валют, отечественного же оборудования европейского уровня пока просто не существует», — расстроен Пресняков.
Инфраструктура
Для достижения наибольшей эффективности производства птицефабрики все чаще обзаводятся собственными газовыми котельными и строят свои кормозаводы. По словам экспертов, 70% сбалансированного комбикорма сегодня производится на заводах, относящихся непосредственно к птицефабрикам, и это является положительной тенденцией, так как повышает качество корма в целом. «Многие хозяйства построили современные комбикормовые заводы, а вот с промышленным производством кормов у нас большие трудности, нужно возрождать отрасль на принципиально новой технической основе», — отмечает Фисинин.
На «Ставропольском бройлере» производят корма на заводах, возведенных еще во времена СССР. При их строительстве использовалось высококачественное оборудование, которое не устарело по сей день. «На нашем кормозаводе изначально, с 1980-х, было установлено очень качественное оборудование фирмы Buhler, которое до сегодняшнего дня не устарело и модернизации не требует. Недавно наше производство расширилось, и мы добавили к двум пресс-грануляторам третий, который также купили у Buhler», — рассказывает Водолазский.
Для ведения эффективного хозяйства также необходимо использование автономных локальных газовых генераторов. По словам Карабанова из «Баси», потери при транспортировке тепла от центральной котельной до корпуса с птицей могут достигать 50% в зависимости от состояния теплоизоляции и удаленности потребителя. Но, размещая котельные в непосредственной близости от корпусов с птицей, можно эти потери минимизировать практически до нуля. Кроме того, КПД современных установок по производству тепла как минимум на 30% выше, чем у старого оборудования, добавляет специалист.
Слова Карабанова подтверждаются опытом «Центрптицепрома». Пресняков рассказывает, что до определенного времени в хозяйстве работала система водяного отопления. «Ранее мы использовали огромную котельную с четырьмя котлами, ее содержание обходилось нам очень дорого. В результате модернизации все помещения были переведены на отопление от локальных газогенераторов, что в разы уменьшило расходы на обогрев предприятия».
Птицеводство на свежем воздухе
В Англии, на экологически чистой ферме «Вуттон», которая принадлежит компании J. C. Bamford Excavators Ltd, освоили технологию, позволяющую выращивать птицу под открытым небом, в загонах, огороженных зеленой изгородью.
Куры в «Вуттоне» содержатся в трех курятниках, каждый из которых вмещает 550 голов. Также оборудовано два курятника для несушек, по 600 птиц в каждом. Пол в курятниках отсутствует: в хозяйстве используются насесты с групповым расположением.
После 80-дневного периода курятники и насесты тщательно очищаются и моются, затем в них помещается новая партия цыплят. На ферме в полную смену работают два специалиста по разведению домашней птицы, время от времени приходят помощники для отлова птиц и заместители основных сотрудников на период отпусков.
До последнего времени на ферме производилось 1650 голов птицы в неделю, однако сравнительно недавно в хозяйство были вложены денежные средства, что позволило провести модернизацию и увеличить производство до 2200 голов в неделю. Увеличился также и средний вес производимого цыпленка, который составляет теперь 1,7 кг. Живьем один такой цыпленок продается за 6 фунтов (около 300 руб.).
Источник: JCB
Менять ли кросс?
Большинство специалистов настоятельно рекомендуют менять кросс птицы после проведения модернизации и перехода на оборудование, способное удовлетворить более «изысканные» потребности птицы, ведь только идеально подобранный кросс поможет использовать весь потенциал новой техники.
Виктор Пресняков, генеральный директор компании «Центрптицепром» (Оренбургская область, агрохолдинг), рассказывает, что в СССР был распространен кросс Смена (по мнению специалиста, неприхотливый, но малоэффективный). Тем не менее, часть российских фабрик, особенно в Уральском регионе, и сегодня используют Смену. Большинство же новых хозяйств работают на более передовых кроссах. Особой популярностью среди аграриев пользуются Росс-308 и Кобб-500. Также Пресняков отмечает, что сегодня все большее распространение получают кроссы Иза-Хаббард (Франция) и Арбор Айкрес (США).
В частности, после проведения модернизации на птицефабриках группы «Черкизово» кросс птицы частично поменялся. По словам Ирины Остряковой, директора хозяйства по управлению коммуникациями и связями с инвесторами, было увеличено количество птицы кросса Кобб, тогда как раньше преобладал Росс и Иза-Хабард.
Новое строительство
В отличие от старых модернизируемых птицефабрик, современные строятся по совершенно новым схемам. Они располагаются на отдельных площадках, в состав которых уже на этапе проектирования входят крупнейшие инкубатории объемом 60-70 млн бройлеров в год, фермы ремонтного молодняка, родительского стада и выращивания бройлеров, причем важным условием является территориальное разделение разных частей птицефабрики. Более того, в каждом из таких хозяйств работают крупные перерабатывающие комплексы, рассказывает президент «Росптицесоюза» Владимир Фисинин.
Именно так, с нуля, в Домодедовском районе Московской области построена компания «Моссельпром». Сегодня это предприятие производит 57 тыс. т мяса птицы в год. Также новой крупнейшей птицефабрикой, возведенной относительно недавно, является «Приосколье» (Белгородская область), где в прошлом году было произведено 178 тыс. т мяса. Таких объемов производства, как в «Приосколье», на «Белой птице» (Белгородская область) никогда не было в Советском союзе, гордится президент Росптицесоюза Владимир Фисинин. Эксперт также отмечает, что Белгородская область является лидером в бройлерном птицеводстве: своей продукцией она снабжает более 10 субъектов РФ, в том числе и такой мегаполис, как Москва.