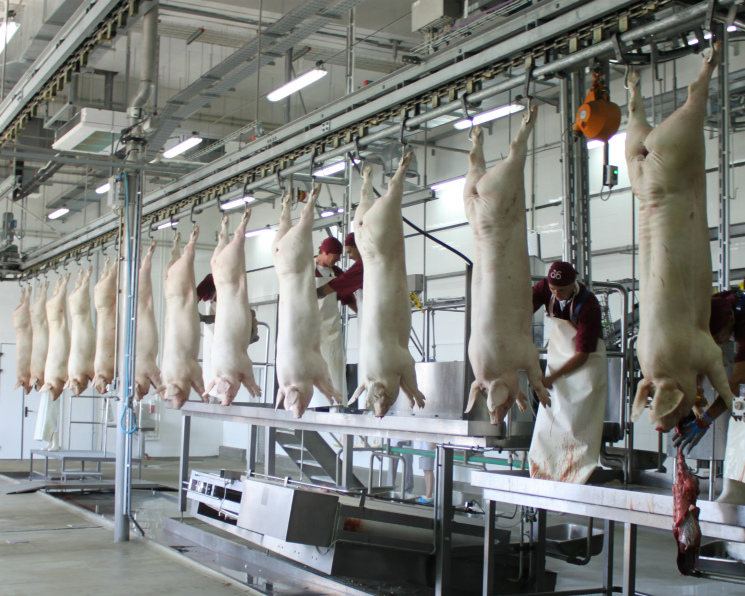
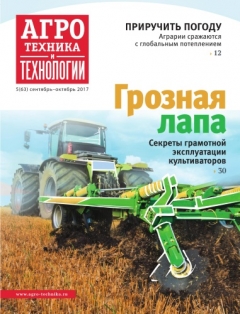
Журнал «Агротехника и технологии»
Рынок убоя и первичной переработки в России развивается достаточно динамично. Драйвером роста выступают крупные свиноводческие агрокомплексы. При этом отмечается интерес и со стороны производителей КРС, которые по уровню оснащения цехов убоя и первичной переработки пока сильно отстают от коллег
Спрос на современные автоматизированные решения заставляет поставщиков оборудования совершенствовать предлагаемые системы по убою и переработке, удовлетворяя требования мясопереработчиков. В том, какие инновации сегодня наиболее востребованы рынком, разбирался корреспондент журнала «Агротехника и технологии».
По причине того, что многие годы убой скота в России не развивался в связи со слабостью животноводства, а технологическое оборудование высокой производительности даже и не разрабатывалось за ненадобностью, в нашей стране не сложилась фундаментальная база производства технологического оборудования для убоя и переработки. Многолетний застой в сфере убоя скота, связанный в первую очередь со слабостью животноводческой отрасли России, и вытекающее из него отсутствие потребности в разработке оборудования высокой производительности не позволили сложиться отечественной фундаментальной базе производства технологического оборудования для убоя и переработки. Поэтому даже небольшие отечественные предприятия вынуждены пополнять основные фонды за счет импортного современного оборудования.
Данный процесс плотно связан с реконструкциями или модернизациями, которые ежегодно проводятся по всей стране, рассказывает Владимир Ермаков, генеральный директор компании «Бансс Евразия» (российское представительство немецкой компании BANSS, специализирующейся на разработке и проектировании комплексных технологий убоя). Впрочем, интерес к зарубежному оборудованию вызван также ростом рынка мясных полуфабрикатов и повысившимися требованиями к срокам годности и внешнему виду продукта, отмечает он. «Иными словами, потребитель заставил производителей открывать новые направления и производства. Ведь идет борьба за качество, которое напрямую зависит от процессов убоя и переработки животных», — объясняет Ермаков.
Действительно, в последние годы многие игроки мясного рынка смогли расширить бизнес и продолжают модернизировать свои мощности, подтверждает Андрей Проконов, коммерческий директор компании «КОММАН» (российский производитель технологического оборудования и готовых решений для убоя и мясопереработки). Немаловажную роль, по его словам, здесь играет тот факт, что мясо и субпродукты стали пользоваться спросом за рубежом. А поскольку экспортные поставки требуют другого подхода к качеству и объему продукции, вопрос модернизации производства для большинства предприятий по убою и первичной переработке скота встал на первое место.
Еще одним не менее значимым фактором являются ответные меры нашего правительства, добавляет Владимир Ермаков. Диверсификация рынков дает четкий толчок для новых быстрорастущих предприятий, а качество является отправной точкой для всех производителей, вне зависимости от имени и объемов выпускаемой продукции.
Кто в лидерах?
Европейские производители мясоперерабатывающего оборудования традиционно лидируют на мировой арене. Прежде всего это Голландия, Дания и Германия. Но в лидерах им, судя по всему, осталось быть не долго.
Сейчас на российский рынок активно выходят японские компании, предлагающие еще более совершенные системы по убою и переработке свиней, замечает Наталья Королькова, генеральный директор «МПЗ Агро-Белогорье» (убойная мощность — 1,8 млн голов свиней в год). Российское же оборудование, по ее словам, пока не конкурентоспособно по отношению к западным производителям и не удовлетворяет потребности современных мясоперерабатывающих предприятий. Исключение составляет разве что производственный софт (программные продукты). В этой сфере российские компании вполне конкурентоспособны, считает Королькова.
Так, на производственных площадках «МПЗ Агро-Белогорье» используется оборудование немецких компаний BANSS и MEATECH, голландской компании MPS, датской HAARSLEV. Таким образом, доля импортного оснащения на этом заводе (если говорить о производственной технологии) составляет 100%. А вот софт — отечественный (разработчик и поставщик — компания «K-Солюшионс»).
«Рынок оборудования постоянно развивается, модернизируется. Всего лишь два года назад, в 2015 году, мы запустили вторую линию глубокой переработки. Но уже сегодня на рынке можно найти еще более продуктивные и экономически выгодные решения. Например, в России появилась возможность точечного решения отдельных задач», — говорит Наталья Королькова. В частности, замечает она, завод «ЗМС-Технолоджи» (совместный проект ГК «Агро-Белогорье» и немецких партнеров) способен производить отдельные части оборудования по аналогии с западными образцами.
В том, что часть оборудования будет выпускаться в России, уверен также Владимир Ермаков. Уже появляются совместные предприятия по изготовлению комплектующих, повысилось качество обработки металла, а школа подготовки специалистов начала выпускать кадры, которые способны конструировать, аналитически мыслить и программировать на необходимых языках. «Мы научились делать элеваторы, прямолинейные конвейеры, санитарно-гигиеническое оборудование, транспортные системы, — поясняет специалист. — Однако не имеет смысла полностью заменять импортное оборудование — на разработку конкурентоспособных образцов уйдут многие годы, российский же опыт слишком мал, чтобы эти вложения могли себя окупить. К тому же, приобретая оборудование, переработчики рассчитывают на технологический трансфер, что помогло бы увеличить производительность и снизить издержки, поэтому намного выгоднее купить импортное оборудование. Таким образом, отрасль выигрывает время и выходит на новые рубежи».
Ермаков считает, что перспектива выхода на зарубежные рынки — прежде всего Юго-Восточной Азии и Китая — заставит наших производителей конкурировать не друг с другом, а с лучшими мировыми предприятиями, причем как по качеству, так и по себестоимости, иначе экспорт будет попросту невыгоден. Поэтому и оборудование надо приобретать с прицелом на будущее — принимать во внимание стоимость владения и долю на килограмм выпущенной продукции.
«Небольшим российским заводам стоит налаживать производство простейших устройств и механизмов, а для этого необходима координация действий и четкий план, чтобы выпускать именно нужные вещи», — уточняет он.
По российским законам
По словам Владимира Ермакова, хотя российский рынок оборудования изобилует компаниями-производителями (есть представители из Европы, США и даже Бразилии), многие просто «морочат голову бизнесу» и тратят время заказчиков. Иными словами, хотят нажиться на доверчивых клиентах.
«Несмотря на то, что поставщиков много, качественных проектов мало, — констатирует он. — Заказчики, за редким исключением, не достаточно компетентны в этой области, чтобы оценить предложенные технологические решения и качество оборудования, и выбирают по цене. Но, как говорится, “жадность порождает бедность” — реконструкции только в 4% заканчиваются успешно, в остальных же 96% здание можно начинать модернизировать заново уже в ближайшие пять лет после запуска».
Проблема в том, объясняет он, что поставщики продают комплекты «железа» в соответствии с формальным техническим заданием заказчика. Заказчик же при этом почему-то надеется получить функционирующий завод на высшем технологическом уровне. При этом у импортеров оборудования нет цели научить наших специалистов работать, ведь они не являются интеграторами технологий, а просто предлагают некий комплект под задачу, как они ее поняли, причем не всегда лучшего качества. Заказчики же требуют модный инжиниринг, но сами не очень представляют, в чем он заключается, и не могут сформулировать, что они хотят получить на выходе. В результате за бешеные деньги получают комплект из нескольких чертежей без обоснований технологических решений и без расчетов, по которым эти чертежи можно проверить. При этом предлагается положиться на некий «опыт» иностранных инженеров. Взяв за основу эти картинки, не проверив решения на выполнимость, люди инвестируют сотни миллионов рублей. Не удивительно, что ошибки и узкие места выявляются на стадии, когда завод уже запущен и исправления даются слишком дорого.
Очень часто иностранные инженеры плохо представляют себе российские особенности. Например, не принимается во внимание, что из-за климатических условий стоимость строительства может быть выше, чем в Европе. Или что необходимо экономить площади, выбирая, возможно, более дорогие, но более компактные решения.
Наталья Королькова указывает на отличия в области проектирования и оснащения убойных цехов в России и в мире, которые связаны со стадийностью проектирования, продиктованной законодательной базой градостроительного кодекса. Российское законодательство наиболее требовательное с точки зрения количества документации, необходимой для выпуска проекта на экспертизу. Причем оценке подвергаются величины, не влияющие на эффективность производства или скорость строительства предприятий, поясняет она.
«В Европе более лояльный подход. При проектировании они внимательнее рассматривают технико-экономические показатели. Российский же законодатель при экспертизе проектов больше оценивает безопасность производства», — сравнивает Королькова.
«Не питайте иллюзий насчет иностранных проектных организаций, все равно будете нанимать российскую компанию, а то и не одну, и переделывать проект под наши нормы», — предупреждает Владимир Ермаков.
При этом, по его словам, большая вероятность, что придется сильно увеличивать площади, чтобы выполнить нормы, а технология может быть искажена, так как не специализированная проектная организация может что-то упустить.
Убойные технологии
В последнее время большим спросом как внутри страны, так и за рубежом пользуется халяльная мясная продукция, делится наблюдениями Андрей Проконов из «КОММАН». В связи с ростом запросов на специализированное оборудование для убоя по технологии халяль многие компании стали разрабатывать и предлагать его на рынке. «Конечно, российские производители внимательно изучают мировые образцы оборудования, и уже есть отечественные разработки, которые по своим качественным и технологическим характеристикам не уступают импортным аналогам, а по стоимостным и вовсе значительно привлекательнее европейских», — считает он.
Михаил Чернявский, руководитель российского представительства финской компании «КОМЕТОС» (поставка модульных предприятий для пищевой промышленности, в том числе мобильных боен) в этой связи указывает еще на одно расхождение норм, принятых в странах Европы и Таможенного союза. Дело в том, что в ЕС современные технологии включают в себя в первую очередь жесткое требование по гуманному убою посредством первичного оглушения тем или иным способом. Поэтому в Евросоюзе полностью запрещен ритуальный убой типа халяль или кашрут, отвергающий по своим нормам эту операцию. У адептов ритуального убоя есть свои резонные возражения, отрицающие негуманность этих традиционных технологий. Поэтому в странах ТС этот запрет отсутствует.
Как рассказал Михаил Чернявский, с развитием в России фермерского способа хозяйствования появилась актуальная задача по сохранению и преумножению результатов трудовой деятельности фермеров-скотоводов. Кроме того, в мае 2014 года вступил в силу новый Технический регламент ТС «О безопасности мяса и мясной продукции», запрещающий реализацию мяса, полученного подворным убоем вне специально оборудованных и сертифицированных убойных площадок (пунктов). В результате встал вопрос о компактных скотобойнях и предприятиях первичной и последующей переработки мяса, соответствующих тем не менее всем требованиям норм регламента.
«С этой точки зрения хорошо себя зарекомендовали комплексы, построенные по модульной схеме, — утверждает Чернявский. — Их отличает быстровозводимость, высокая гибкость в соблюдении требований ТЗ заказчика, возможность расширения и определенная мобильность».
По его словам, практика последних десятилетий показала высокую эффективность модульного способа строительства скотобоен для предприятий с небольшой мощностью. При этом разработаны конструкции с широким спектром производительности и большим диапазоном технологических операций. «Например, в составе предприятия может быть один модуль с ежедневной производительностью 6-8 голов КРС, 20-25 голов свиней или примерно 40 голов МРС. А может быть предложено решение с производительностью несколько десятков голов КРС или сотен голов свиней и МРС в смену», — объясняет руководитель российского представительства «КОМЕТОС».
С ним не вполне согласен Андрей Проконов. «Интерес к так называемым модульным заводам по убою скота и переработке мяса небольшой производительности сохранялся довольно долго. Однако в настоящее время спросом пользуются только комплекты оборудования, которые заказчики устанавливают в стационарные здания», — возражает представитель «КОММАН». По его мнению, это связано как раз с тем, что модульные цеха не могут в полной мере соответствовать требованиям Технического регламента Таможенного союза «О безопасности мяса и мясной продукции» (ТР ТС 034/2013).
При этом он уточняет: необходимо определиться, что имеется в виду под понятием «модульной» бойни. Как рассказал Проконов, российские производители предлагают на рынке модульные бойни контейнерного типа и модульные бойни из быстровозводимых металлоконструкций. Под первыми подразумеваются контейнеры размером 2,6 метра на 6 или 12 метров с установленным внутри оборудованием для убоя скота. Их производительность невелика, а согласно упомянутому выше техрегламенту, на таких предприятиях должны быть предусмотрены производственные участки, которые уместить на столь малой площади невозможно. В связи с этим требуются дополнительные модули, где будут размещаться все необходимые технологические участки. Но когда из модулей собирается полноценный убойный цех, его стоимость оказывается сопоставимой со стоимостью второго варианта — модульного здания из быстровозводимых металлоконструкций, которые прочно связаны с фундаментом.
На сегодняшний день строительство зданий из быстровозводимых конструкций освоено во всех регионах России. Стоимость таких конструкций гораздо ниже, чем капитальных зданий из кирпича или бетонных плит, к тому же они значительно проще в технологическом плане. Кроме того, в таких зданиях гораздо больше свободного пространства, что обеспечивает более комфортную и менее травмоопасную работу, а также позволяет предусмотреть все необходимые технологические помещения, обращает внимание Андрей Проконов. «На мой взгляд, модульные бойни из быстровозводимых конструкций в перспективе будут основной моделью убойных предприятий, — говорит он. — Но отказываться от модульных боен контейнерного типа нецелесообразно. Есть очень много регионов Крайнего Севера, Сибири, Дальнего Востока, где модульные бойни контейнерного типа — единственный экономически обоснованный вариант убойного цеха».
Поскольку современные технологии убоя подразумевают гуманное отношение к скоту, в том числе в предубойной фазе, интерес представляют передвижные или мобильные скотобойни на базе автошасси, полозьев (для условий Крайнего Севера) или на плавсредствах, продолжает тему Михаил Чернявский. Применение подобных комплексов, по его словам, позволяет избежать стресса у животных во время их перевозки к убойному пункту — скот остается в привычных условиях, а это, помимо прочего, еще и положительно влияет на качество мяса.
Один из самых инновационных и гуманных методов обездвиживания животных — погружение их в камеры с углекислым газом (СО2) — применяют на Курском мясоперерабатывающем заводе (входит в ГК «АгроПромкомплектация»; производственная мощность — 5100 голов в сутки). «База предубойного содержания предприятия включает в себя две рампы для одновременной выгрузки поголовья из двух транспортных средств. Для быстроты и удобства процесса выгрузки рампы оснащены доклевеллерами», — рассказывает Денис Бартенев, заместитель директора Курского мясоперерабатывающего завода.
Также к базе предубойного содержания относится прогонный коридор, позволяющий выявить травмированных и подозрительных животных, продолжает он. Помещение предубойного содержания подразделяется на 9 секций для выдержки животных. Вместимость каждой — 140 голов. Поэтому в БПСД одновременно может быть выгружено 7 партий животных (7 скотовозов по 180 голов).
Сам же процесс перемещения животных в камеру оглушения осуществляется полуавтоматически через прогонный путь, способствующий равномерной загрузке животных в бутину по 6 животных, где оглушение свиней происходит наиболее гуманным способом — газовоздушной смесью с повышенным содержанием углекислого газа, говорит Бартенев.
Еще одной особенностью современного убоя являются высокие санитарно-гигиенические требования, отмечает Михаил Чернявский. Это касается как материалов, из которых делаются рабочие поверхности, включая покрытие стен, так и одобренных для пищевой промышленности марок нержавеющей стали и пластиков, которые идут на изготовление узлов механизмов и инструментария.
С этой же целью, продолжает он, применяются различные ноу-хау типа создания избыточного давления воздуха в производственных цехах, встроенных систем их мойки после окончания смены, пунктов помывки рабочей обуви, индивидуальных стерилизаторов инструмента персонала
Правило пяти «Э»
Сегодня все мясопереработчики стараются максимально автоматизировать свое предприятие, чтобы сократить возможные риски и достичь конечной цели, но все же цена оборудования при принятии решения является важным фактором. Однако, сэкономив на стоимости линии убоя, предприятия экономят на самих себе. «Это все равно, что покупать ботинки 44 размера вместо 45-ого, а к ним еще в придачу и средство для растяжки кожи — ну и в чем же здесь экономия?» — иронизирует Ермаков.
Стоимость нового завода (в зависимости от мощности и сложности) составляет от 2 до 4 млрд руб., подсчитывает он, а экономия на линии убоя в процессе покупки, как правило, не более 300 тыс. евро. А что дальше — опять докупать спрей для растяжки из резервного фонда? Поэтому, продолжает специалист, есть золотое правило: сделай грамотный проект, подготовь развернутый тендер, а потом покупай то, что тебе действительно необходимо, и не экономь на качестве, т.к. настоящее качество неповторимо.
Передовых мясоперерабочиков много, а вот предприятий по убою, которые не испытывали бы проблем с качеством, можно по пальцам пересчитать, утверждает Ермаков. Дело, по его мнению, в том, что многие умалчивают о качестве убоя, но профессионалы отрасли, в особенности специалисты отделов сбыта или закупок, прекрасно знают, где нужно покупать мясо, течет оно или стабильное, что из него можно сделать и какой по качеству и срокам годности получится продукт на выходе.
Среди лидеров по внедрению инноваций, которых можно смело приводить в пример, Владимир Ермаков отмечает такие предприятия, как «Агро-Белогорье», «Заречное», «АгроПромкомплектация», «Останкино». Но самое передовое предприятие, аналогов которому в стране по-прежнему нет, — АПХ «Мираторг», считает он.
Михаил Чернявский обращает внимание, что основными задачами внедрения высокотехнологичных систем убоя являются эффективность инвестиций, высокое качество продукции с длительными сроками реализации, снижение затрат и доли ручного труда, повышение уровня гигиены и технологичности производства. В принципе, подчеркивает он, предела совершенству просто не существует, на рынке есть предложения линий очень высокой производительности от ведущих компаний, которые ни в коем случае не поступятся качеством выпускаемой на их оборудовании продукции.
Как правило, в последние годы разработки ведутся, исходя из различных потребительских запросов, уточняет Чернявский. Для крупных производств основной тренд — снижение доли ручного труда, автоматизация и оптимизация процессов. Для специализированных, но небольших предприятий — это оптимизация процессов, универсальность производств, высокая гигиена, короткие сроки реализации проектов, надежность оборудования, программы обучения, поддержка продаж (в том числе экспорта), создание своего уникального продукта на рынке. Для совсем маленьких хозяйств основной фактор — дешевизна и простота оборудования (обычно отечественного производства), заполнение основных прорех в выполнении санитарных требований.
А для средних предприятий, где невозможно применить дорогие роботизированные решения, крайне важным является эргономика и универсальность, например, когда на комбинированных линиях малой производительности обрабатываются разные виды животных, добавляет Владимир Ермаков. Такие линии занимают меньше места и не требуют больших инвестиционных затрат. Эргономика достигается за счет подъемно-опускных платформ и специального оборудования рабочих мест.
«При небольшой производительности разумно и экономически выгодно приобрести бокс оглушения, шпарчан, обезволашивающую машину для обработки поверхности, конвейер и ручной инструмент импортного производства. Все остальное — платформы, гигиену, лотки и пр. — купить отечественные», — рекомендует он. Таким образом, заключает Ермаков, стоимость оборудования можно сократить в среднем на 15%. А на сэкономленные деньги лучше купить не оцинкованное, а нержавеющее импортное оборудование, которое прослужит дольше.
По словам Натальи Корольковой, при выборе подходящей технологии в первую очередь нужно учитывать стратегическую цель компании. На каком рынке, с каким продуктом планирует работать компания в перспективе (8-10 лет от старта). Исходя из этого и подбирается подходящая технология.
«Прежде всего, линии должны быть безопасными, — делится опытом руководитель «МПЗ Агро-Белогорье». — Ведь мы работаем с ножами и пилами. Кроме этого, оборудование должно обеспечивать максимальную сохранность продукта. Пильные полотна не должны быть агрессивными, чтобы максимально сохранить мышечное волокно при распиле. Потери на линиях должны быть минимизированы. В этом направлении производители постоянно совершенствуют свой опцион. Изменяют углы наклона, унифицируют сами пилы, их движущий механизм, реверсы и так далее».
В целом успех проекта, обобщает Михаил Чернявский, определяется Правилом пяти «Э»: 1) эффективность по выходам, 2) экономика производства, включая логистику, квалификацию персонала и менеджмента и региональные особенности, 3) экономичность по затратам, 4) эргономичность по организации производственного процесса и комплектации, 5) экология предприятия.
Робот или простой автомат?
Роботизация — это будущее, которое совсем близко. Пока из-за высокой стоимости подобное оборудование могут позволить себе лишь крупные предприятия, говорит Андрей Проконов, но в ближайшее время обязательно появятся роботизированные линии убоя скота и переработки мяса, которые либо совсем исключат участие человека в процессе, либо существенно сократят применение физического труда.
Производительность линии — это скорость обработки туши или полутуши, объясняет Владимир Ермаков. Ручной труд оптимален на производительности до 250 свиней в час, 40 КРС в час или 120 МРС в час. Назовем это порогом, после которого необходимо удваивать количество рабочих мест и строить здание значительно больших размеров. А высокотехнологичные системы, то есть роботы, позволяют сократить количество персонала и сохранить размеры здания. Таким образом, подчеркивает он, решаются несколько задач. Во-первых, здание имеет оптимальные размеры, а это означает, что эксплуатационные затраты не будут расти. Во-вторых, повышается точность и качество обработки, что сказывается на общем качестве готовой продукции. В-третьих, возможно увеличить скорость до 700 голов свиней в час. Для сравнения — это 75 трехъярусных грузовиков за 16 рабочих часов.
С точки зрения собственно оборудования, самые перспективные разработки — робототехника, уверен Ермаков. Сейчас для России робот, разделывающий на предприятии свинью, — что-то просто фантастическое. Большинство отечественных заводов оснащено не роботами, а самыми простыми автоматами, но, надо сказать, разница между этими двумя видами оборудования колоссальная, уверяет специалист.
Робот стоит дороже автомата: средняя цена одной машины около €360-370 тыс., и это только за железо, приводит цифры Ермаков. А к нему еще необходимо добавить ПО (€150 тыс.) и ежегодное обслуживание, которое состоит из запасных частей и расходных материалов (€30 тыс.), приезда специалистов (€20 тыс.), собственного технического персонала (€15 тыс.). Итого на круг получаем порядка €600 тыс.
Для сравнения, автомат стоит в 2,5 раза дешевле. Конечно, это заманчиво на стадии покупки, однако потом возникают проблемы, предостерегает Ермаков. Дело в том, что автомат — это автоматическая машина, которая выполняет команду четко по заданной траектории. Машина не думает, а значит, и назвать ее роботом никак нельзя. Отсюда возникают и все основные проблемы — неровный рез, распил, надрез и пр. Это связано с тем, что мы все-таки работаем с сырьем животного происхождения, которое не так просто стандартизировать на стадии окорма и выращивания, поясняет специалист. В одной партии свиней с одной и той же фермы могут поступать совершенно разные животные по весу, упитанности, возрасту и структуре. Соответственно, на конвейере их никто не будет сортировать и перестраивать каждый раз работу автомата, а значит, процент брака будет варьироваться в среднем от 20 до 37%.
Второй момент, на который указывает Ермаков, — повышение нагрузки на персонал, который должен дорабатывать за автоматом. Ведь каждый неверный рез — это необходимость ручной дозачистки или распила, что напрямую ведет к третьему минусу — качеству исходного сырья и срокам годности готовой продукции.
Робот же, благодаря системе сканирования туши, полутуши или отруба, всегда обращается к базе данных и выбирает из памяти аналогичное по структуре, весу и упитанности животное и делает самый точный и нужный разрез, отмечает Ермаков. При этом, подчеркивает он, база данных постоянно обновляется и корректируется под нужды заказчика по его же собственным животным. Дорабатывать полутушу нет необходимости, соответственно, лишний раз данное мясо человек руками не трогает, а доля контаминации снижается.
Единственное полностью роботизированное производство в России организовано на предприятии свинокомплекса «Короча» компании «Мираторг», утверждает Ермаков. В «Короче» ежедневно забивается до 10 тыс. свиней.
«На Курском мясоперерабатывающем заводе наиболее трудоемкие операции тоже выполняются роботами, — замечает Денис Бартенев. — Это распил лонного сращения тазовой кости и надрез туши вдоль белой линии живота, разруб грудины и брюшины, разруб вдоль позвоночника».
На заводе «Агро-Белогорье», по словам Натальи Корольковой, робототехника применяется в основном на линиях обвалки и упаковки. «В ближайшее время у нас есть планы по наращиванию мощностей на линии убоя, — делится она. — Увеличится скорость на существующей линии, в том числе за счет введения в производственный процесс робототехники, которая будет осуществлять распил на полутуши, отсечение головы и выемку органов».
ПО — важный инновационный фактор
Еще один важный инновационный фактор — широкое применение в управлении процессом автоматики, электроники и специального программного обеспечения для работы устройств ПЛК (PLC — Programmable Logic Controller), говорит Михаил Чернявский.
Он подчеркивает, что благодаря внедрению этих технологий можно кардинальным образом оптимизировать и автоматизировать рабочий процесс. Ведь основной режим работы ПЛК подразумевает его длительное автономное использование без серьезного обслуживания и практически без вмешательства человека.
На Курском мясоперерабатывающем заводе в процессе производства применяются лучшие зарубежные IT-технологии пищевой промышленности. «Благодаря передовым инновационным IT-решениям мы способны эффективно управлять производством, оперативно анализировать важнейшие финансовые показатели, — говорит Бартенев. — Процесс полностью контролируется на всех стадиях: от убоя и обвалки до отгрузки готовой продукции. Все это повышает не только качество продукции, но и рентабельность». В будущем технический потенциал, заложенный в КМПЗ, позволит увеличить выпуск мясной продукции в два раза.
Кстати, как рассказал руководитель КМПЗ, в цехе убоя оглушенные свиньи подвешиваются на путовую цепь для автоматизированной обработки в ходе перемещения по подвесному пути. Скорость перемещения — 300 голов в час. При перевешивании туши на разногу ей присваивается номер внутри партии и автоматически измеряются параметры туши для последующего категорирования. Перед размещением туши в камере охлаждения автоматически наносится идентификационный номер (определяющий принадлежность к партии), категория и товароведческое клеймо, а также выполняется взвешивание туши.
Для получения мяса высокого качества Курский мясоперерабатывающий завод использует полностью автоматизированную уникальную систему воздушно-капельного охлаждения с последующим созреванием полутуш в камере хранения при температуре 0…+2°С.
«Охлаждение полутуш у нас двухфазное: сначала гидроаэрозольное, а затем — доохлаждение в камере созревания, где туши распределяются автоматически согласно категории, — объясняет Бартенев. — Из камеры созревания автоматически по FIFO они выгоняются после охлаждения на предварительную разделку, взвешиваются, отсекаются голова, ноги, и полутуши направляются на отгрузку или на подготовку отрубов (в соотношении 50 на 50%). Отгрузка полутуш осуществляется только согласно заданию в системе сканированием штрих-кода».
«Наши холодильники для созревания и хранения полутуш не используют человеческого труда. То есть все конвейерные приводы управляются программным продуктом, и туша после идентификации самостоятельно направляется на нужную ветку», — присоединяется к обсуждению Наталья Королькова. По ее словам, это помогает отсортировать полутуши по определенным стандартам и с разделением потоков: на клиента или на обвалку. При этом все процессы автоматизированы. Программа контролирует время пребывания туши в холодильнике для созревания и дальнейшего хранения с указанием предельных значений по данным процессам.
Спецификой работы крупных перерабатывающих предприятий является также потребность в учетных системах, которые на стадии разделки туши способны определить процент содержания ценных частей и критерии постности мяса, продолжает Королькова. Это нужно для того, чтобы принимать решения о классификации глубины разделки на участках обвалки. «На этом рынке среди поставщиков классификационного оборудования явственно выделяется датская Carometec с прибором AutoFom», — отмечает она.
По словам Владимира Ермакова, отечественный рынок близок к прорыву в области программного обеспечения в сфере ERP систем управления на предприятиях по убою и первичной переработке животных. «Постепенно происходит вытеснение дорогостоящих так называемых программ-прослоек, которые, по мнению иностранных коллег, являются самыми передовыми, функциональными и клиентоориентированными. На самом деле это не всегда так, — утверждает Ермаков. — Любое программное обеспечение должно быть настроено в соответствии с бизнес-процессами заказчика и интегрировано с другими системами предприятия — бухгалтерскими и управленческими программами». Кстати, стоимость таких настоек и доделок может значительно превышать первоначально заявленную стоимость ПО.
Практика показала, что для обслуживания такого рода ПО необходим штат высококвалифицированных специалистов именно по этим программам, которых в России еще нет, а с иностранными специалистами надо рассчитываться в валюте. Интеграция же с бухгалтерскими системами — постоянный процесс, для чего требуется постоянная поддержка.
«Сейчас компания 1С озадачилась отраслевыми решениями и создала Центр компетенции на базе компании “Абсолют СОФТ”, — говорит Ермаков. — Cначала появился модуль 1С “Мясокомбинат”, далее было написано “Управление производством”. Вместе с ПО поставляются и промышленные рабочие станции, оборудованные современными компьютерами и мониторами, которые ни в чем не уступают иностранным аналогам». По его словам, интерфейсы даже более привлекательные и удобные, а интеграция с 1С — бесшовная. Это и есть самое важное импортозамещение: не скопировать железку, а заместить мозги и набираться ума-разума, нарабатывать ноу-хау всем вместе.
Наталья Королькова поддерживает коллег. По ее словам, роботизация и программирование — наиболее интересные и перспективные направления, которые способны дать конкурентные преимущества как при создании, так и при модернизации производства. «Здесь открываются большие перспективы для российских программистов и ученых, — обращает внимание генеральный директор «МПЗ Агро-Белогорье». — Молодежь, которая работает в этом направлении, нужно сохранять в стране, создавать благоприятные условия работы».